PIPING SOLUTION: Ultra Tech
MARKET SEGMENTS: Cement plant processing
CUSTOMER: Rexweld
LOCATION OF PROJECT: Great Plains, USA
APPLICATION: Pneumatic cement dust line
ENVIRONMENT: Cement plant
PRODUCTS USED: Ultra 600 custom fabrication and engineered solution
SOLUTION:
Rex Waller, principal at Rexweld, called Ultra Tech Business Development Manager, Doug Mortola, to discuss a challenge his customer was facing. The issue was at a cement plant in the Great Plains region. The facility had a complex fitting in their pneumatic dust line which was encased in concrete many years earlier to plug a leak in their mild-steel pipe. The plant Maintenance Team required a better solution capable of withstanding the low pressure, abrasive cement dust. Unfortunately, there were no engineering drawings and accurate measurements were unavailable while the pipe was encased in concrete.
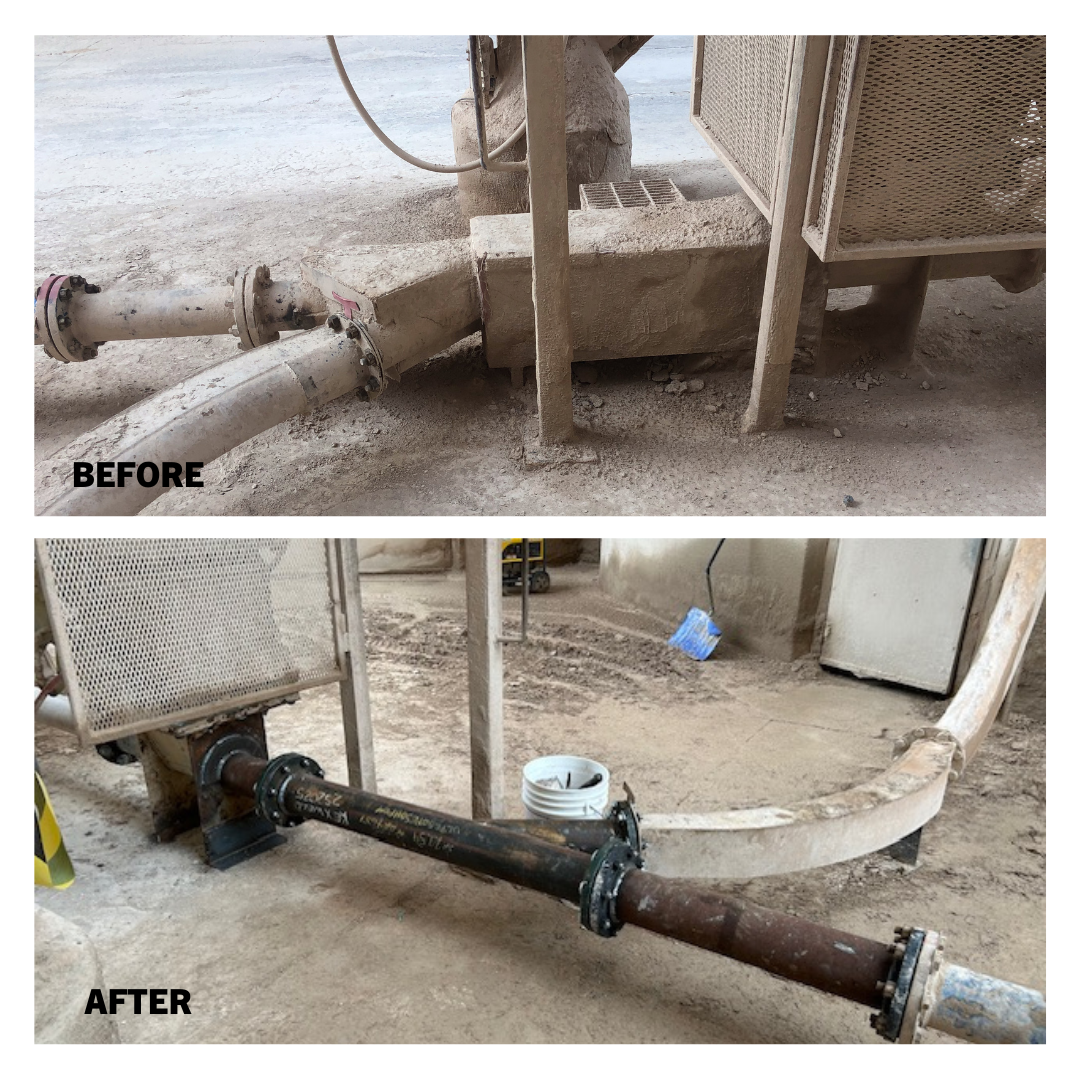
Doug brought a picture and the challenge to one of our engineering “MacGyvers”. The Ultra Tech engineering team have decades of pipeline design experience in AutoCAD. They evaluated the image and the single measurement of a straight section between two flanges. Using AutoCAD, the team drafted an approval drawing based on the image and their exceptional experience designing solutions for a wide variety of applications.
The drawing was approved, and Doug managed the piece through the Ultra Tech design and QC process. When the new Ultra Tech fitting arrived on-site, the concrete and old pipe were extracted. The new Ultra 600 wye was a perfect fit and the customer was thrilled!
The Ultra Tech team takes great pride in being “Partners in Problem-Solving” for our customers.