Everyone who operates in the aggregate business knows that aggregate processing equipment is subjected to some of the highest levels of wear and tear in industrial operations. Crushing, screening, and transporting aggregate is a fundamentally abrasive process, which can lead to frequent breakdowns, costly maintenance and downtime.
That is why leading aggregate suppliers install abrasion-resistant (AR) steel plates in their production lines. These specialized steel plates are designed to deal with the uniquely high levels of wear and tear that aggregate equipment experiences on a daily basis. In this article, we delve into exactly how you can maximize the lifespan of your aggregate processing equipment with AR steel–including specialty steel plates like Tri-Braze®.
Understanding the Role of Abrasion Resistant Steel Plates in Aggregate Operations
Abrasion-resistant steel plates are not your normal steel plate. They are specially engineered to withstand high levels of abrasion and impact forces, allowing them to last much longer than traditional steel plates. Specialty AR steel plates, such as Tri-Braze, are uniquely suited to absorb the incredibly high levels of impact and abrasion that comes with handling and processing rough materials, including aggregate. Aggregate operations often use Tri-Braze in high-wear areas, like crushers, hoppers, chutes, and conveyor systems.
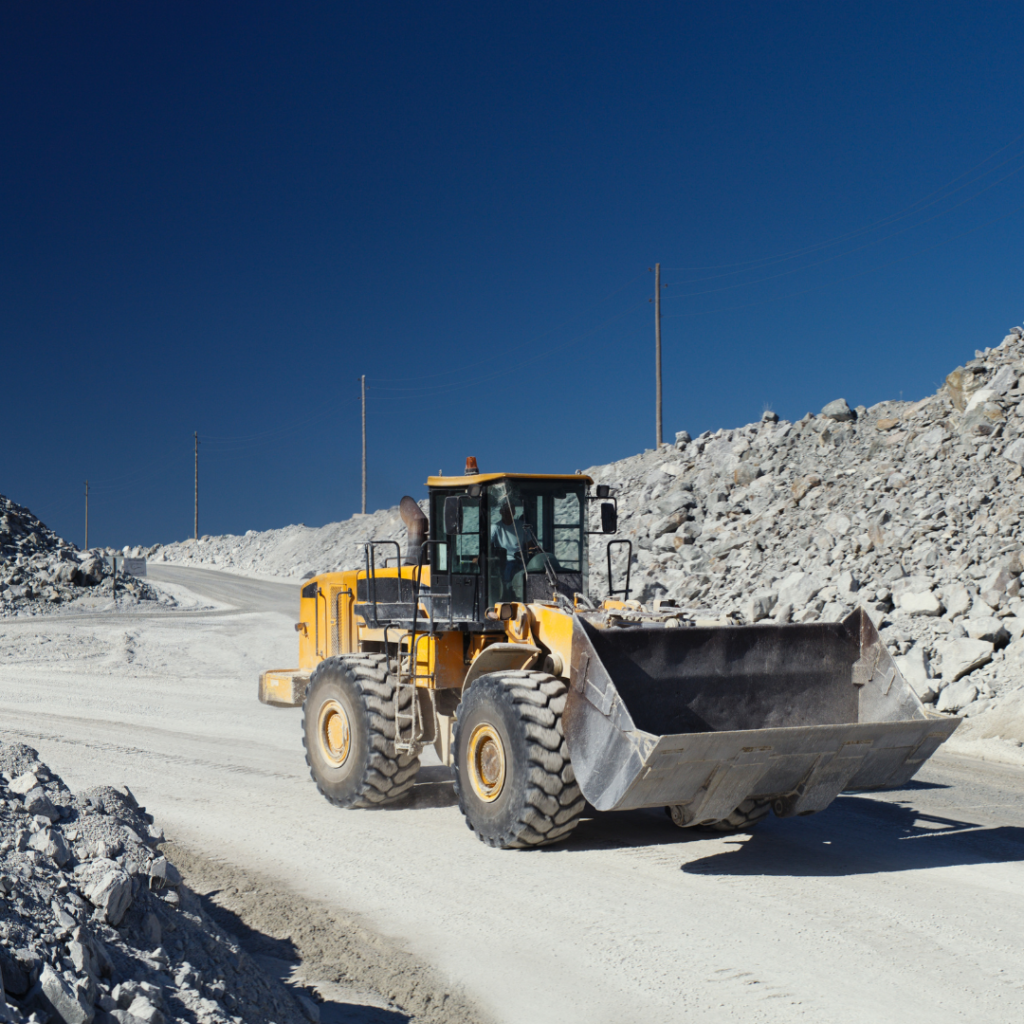
In the aggregate processing operation, AR steel plates act as a sort of sacrificial layer, shielding the underlying equipment and components. When traditional steel plates are used rather than AR steel, equipment wears down at a much faster rate, leading to increased downtime and more frequent maintenance/repairs that disrupt production.
Three Key Benefits of Using Specialty AR Steel Plates for Aggregate Equipment
The most obvious benefit of implementing specialty AR steel, such as Tri-Braze, in your aggregate processing system is the long-term cost savings. When you implement AR steel plates in your operation, you have to replace key pieces of equipment and components less frequently, which can save considerable amounts of money.
Additionally, specialty AR steel plates like Tri-Braze help you go longer between costly repairs and maintenance. This means that your operation can be running for longer periods, allowing you to repair equipment according to the schedule that works best for your operation.
Another huge benefit of specialty AR steel is a safer work environment for your employees. When equipment suffers fewer breakdowns and needs fewer repairs, employees are placed in fewer unsafe or precarious positions, which helps foster a safer work environment.
Applications of AR Steel Plates in Aggregate Equipment
We’ve helped aggregate operations identify the key areas to implement specialty AR steel plates in order to get the most long-term value. In the aggregate industry, we’ve found that these key areas include:
Crushers
Crushers are responsible for breaking down large rocks, which means they experience some of the highest levels of abrasion and impact in the entire process. By lining the crusher sidewalls with specialty AR plates, you can shield the critical components of the crusher from excessive wear, allowing you to get a much longer useful life out of your equipment.
Screens & Conveyors
Screens and conveyors are key pieces of equipment for transporting aggregate throughout the processing operation. They are subjected to high levels of abrasion at every turn. Truck dump screens, rotary screens and screen decks can all be fabricated from Tri-Braze. Installing specialty AR plates on conveyor pans and skirt board liners reduces the erosion created by friction and material impact.
Chutes and Hoppers
Chutes and hoppers are key for funneling and storing aggregates and are another key area where specialty AR steel can be incredibly useful. These pieces of equipment can withstand high levels of abrasive materials moving at high speeds, which can accelerate wear and tear damage. By lining chutes and hoppers with specialty AR steel plates like Tri-Braze, you can slow down the wear of these components and ensure the smooth handling of aggregate materials.
Best Practices for Implementing Specialty AR Steel Plates in Aggregate Operations
Even specialty AR steel plates do eventually fall victim to wear and tear and need to be replaced. However, you can extend the life of your AR steel by following our best practices, including:
Proper Installation
Proper installation is key when it comes to implementing specialty AR steel plates in your aggregate processing operation. AR steel plates need to be placed in the areas that experience the highest levels of wear and tear, and properly attached to prevent them from loosening during operation. Installing your Tri-Braze steel plates in the highest wear areas with the proper welds or bolts will help you realize the reduced Total Cost of Operation (TCO) that the right AR steels can provide.
Regular Inspection and Maintenance
Just because you implement an AR steel plate doesn’t mean you can stop monitoring it. After all, specialty abrasion-resistant steel plates still wear over time, just at a slower rate than traditional steel. This means it’s still important to keep an eye on your equipment by conducting routine inspections that monitor wear levels. Doing so will also help you put together a proper maintenance schedule, allowing you to replace more parts when it’s convenient for you, not just when something breaks.
Choosing the Right Supplier
Choosing the right supplier is always key. Tricon Wear Solutions has been a pioneer in the specialty AR steel industry for decades. Not only can we deliver the highest quality specialized AR steel on the market, but we can also share the expertise of our engineering and field sales teams that can help you properly implement your Tri-Braze steel plates and get the most from your investment.
Partner With Tricon Wear Solutions
Abrasion-resistant (AR) steel plates are an essential investment for aggregate producers looking to maximize equipment lifespan, reduce downtime, and improve overall profitability. By utilizing AR steel plates like Tri-Braze and Super-C in high-wear areas such as crushers, hoppers, chutes, and conveyor systems, aggregate operations can significantly extend the life of their equipment, and minimize costly maintenance and repairs.
If you are ready to take your aggregate operation to the next level, partner with Tricon Wear Solutions. As a leading provider of specialty AR steel plates and wear solutions, Tricon Wear Solutions has the expertise and experience to help you identify the best places to implement AR steel plates in your operation and get the most bang for your buck.