The mining industry is one of the toughest manufacturing industries for industrial equipment. This is because your machines are constantly being exposed to some of the harshest conditions and most abrasive materials on earth. Additionally, mining equipment is expensive, with key pieces often costing several hundred thousand (sometimes even several million) dollars. That’s why using the best abrasion-resistant wear plate is pivotal to protecting your mining equipment and getting the most out of its useful life. In this article, we’ll delve deep into some of the best ways you can use abrasion resistant plates to protect and extend the life of your mining equipment.
What are the Benefits of Using Alloyed Abrasion Resistant Wear Plates for Mining?
Alloyed abrasion resistant wear plates provide several benefits for mining operations:
- Longer Usable Life: Alloyed wear plates are through-hardened and protect important components from the heavy wear and tear you can expect in the mining industry, extending the life of your equipment.
- Lower Maintenance Costs: Since alloyed, through-hardened plates help extend the usable life of your equipment, repairs are less frequent and can be scheduled more predictably.
- Higher Efficiency: Alloyed abrasion resistant wear plates allow your equipment to be up and running for longer, making your operation more efficient.
- Cost Savings: Improved efficiency in your operations helps drive down unit costs, despite the higher upfront costs associated with using alloyed AR wear plates.
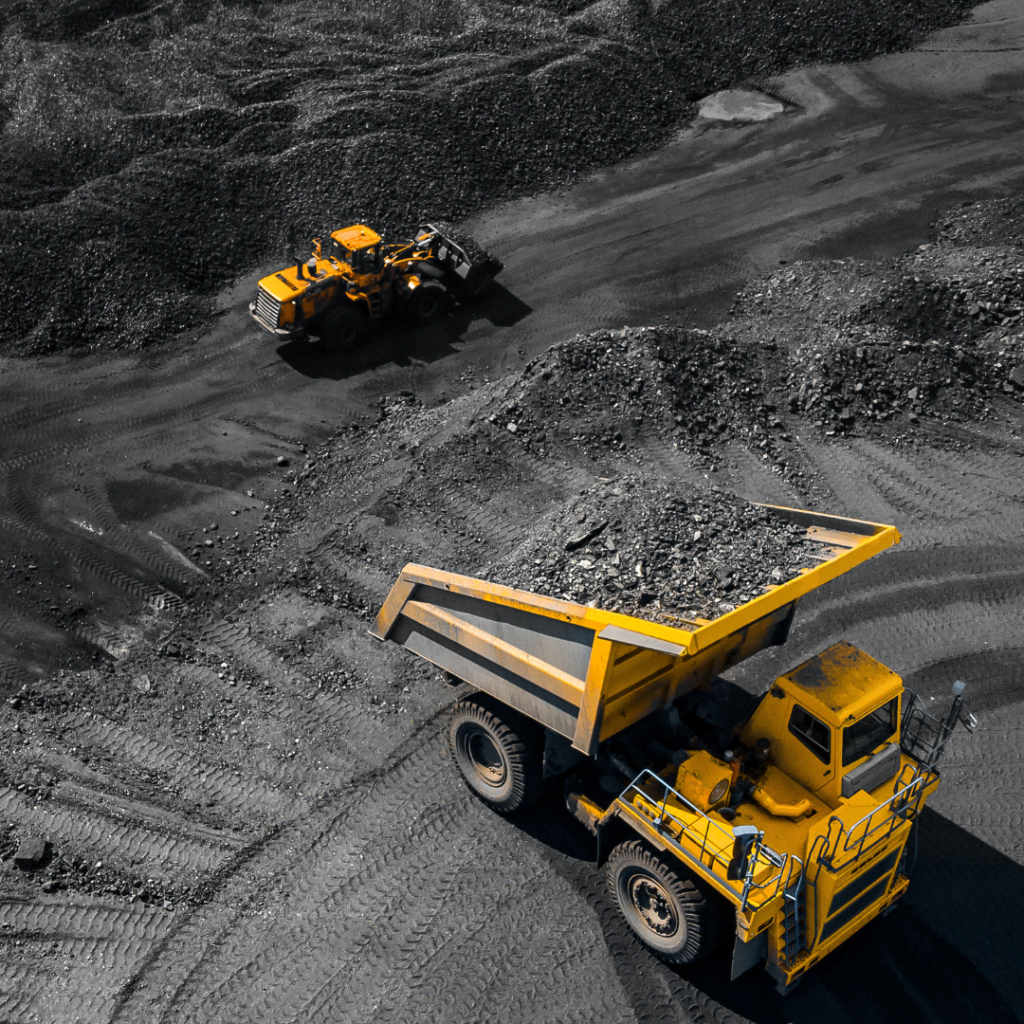
Overall, abrasion resistant wear plates have become a staple in the mining industry, with most businesses finding that they have become an indispensable part of their day-to-day operations. Although they come with a slightly higher investment upfront, the benefits far outweigh the costs associated with upgrading to abrasion resistant plates.
What are the Most Common Applications of Wear Plates in the Mining Industry?
Below, we’ve put together a list of the six most common areas we see our clients using Tri-Braze ® alloyed abrasion resistant plates, and why they choose to use them.
- Conveyor Systems: Conveyor systems are one of the most pivotal parts of a mining operation. Since they’re designed to move material without the constant oversight of an operator, it’s important that conveyors stay online for as long as possible. Tri-Braze® skirt boards and pan liners can help keep your conveyors up and running with less down time by acting as a sacrificial layer, allowing a much longer lifecycle for your system.
- Crushers: Breaking down large rock and ore into more manageable sizes is not an easy job, which means that crushers see some of the most intense wear and tear out of all of the equipment at a mine. When implemented correctly, abrasion resistant liners and screens can help extend the amount of time between repairs and maintenance, allowing your operation to stay running longer.
- Excavator/Loader Buckets and Dozer Blades:Tri-Braze® and Super-C® wear plates are also very useful when it comes to earth-moving equipment like excavators, loaders, and dozers. The constant moving of materials can wear down these pivotal pieces of equipment quickly. Bed liners, bucket liners and dozer blades fabricated from Tri-Braze allow you to go longer periods of time without having to swap out buckets, leading to higher efficiency and an overall safer workplace for your employees.
- Hoppers and Chutes: Hoppers and chutes are a literal bottleneck in your operation, holding large quantities of material. These pieces of equipment can also experience incredible levels of abrasion thanks to the considerable weight of the material and its abrasive nature. This makes hoppers and chutes both prime targets for abrasive wear. Using Tri-Braze® alloyed wear plates in hoppers and chutes can help cut down the frequency of replacing parts, leading to a smoother operation.
- Truck Beds: Haul trucks that work within mines are subjected to some of the harshest and most abrasive conditions in a mining operation. The combination of impact from loading and abrasion from dumping causes a considerable amount of wear and tear to their beds. Tri-Braze® wear plates can help extend the lifespan of the truck beds when compared to the same thickness AR wear plates, giving the same service life with thinner liners, leading to less carry-back weight, longer tire life, and better fuel economy.
- Ball Mill Liners
Ball mills are used to grind materials and crush them into smaller pieces for further processing to separate the desired ore from its surrounding material. The grinding operation creates a huge amount of abrasion, both from the ore-laden material and the grinding balls in the mill. Tri-Braze® and Super-C® wear plates have been proven to outlast traditional AR wear plates, enhancing uptime and mill throughput.
Tricon Wear Solutions: A Trusted Partner in the Mining Industry
The mining industry relies on some of the most sturdy, reliable, and complex equipment in the field. Wear plates not only play a pivotal role in helping protect your company’s equipment from everyday wear and tear, but they also play an important role in employee safety. After all, when your equipment requires less maintenance, your production lines can stay up and running for longer and your employees will find themselves in hazardous positions less often.
Tri-Braze® alloyed, abrasion-resistant wear plates provide critical protection to some of the most important pieces of machinery experiencing the highest levels of wear and tear. By investing in the highest quality wear plates from Tricon Wear Solutions, you can enhance both the profitability and safety of your operation.