The pulp and paper industry plays a vital role in the global economy, providing consumers with many essential paper products: tissue paper, paper towels, brown paper, printer paper and packaging materials.
To produce these goods, paper mill operators rely on manufacturing processes that can be harsh and demanding on their expensive equipment. Downtime and maintenance costs can be incredibly costly to pulp and paper operations.
To reduce wear and tear on their equipment, pulp and paper businesses have increasingly adopted abrasion-resistant steel plates to help their equipment last longer, operate more efficiently, and reduce time between repairs. Many of these businesses turn to Tricon Wear Solutions for advanced materials customized to their needs.
We’ve put together an overview below to help you understand just how abrasion-resistant steel technology helps businesses in the pulp and paper industry.
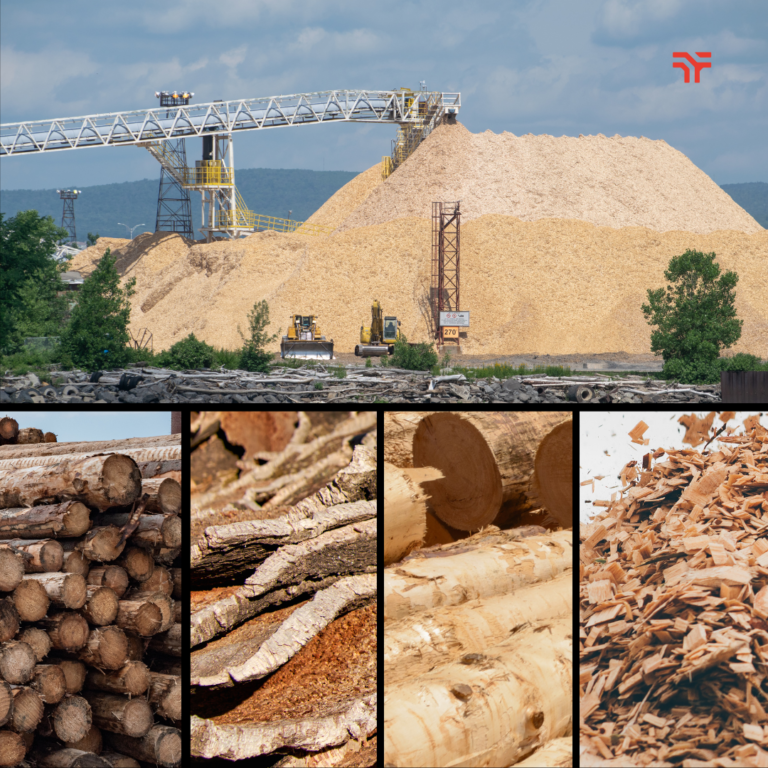
Challenges in the Pulp & Paper Manufacturing Process
- Before you can understand how AR steel helps the pulp and paper industries reduce wear and tear, it’s important to understand why equipment in these industries is subjected to so much impact and abrasion in the first place. Some of the key areas exposed to wear include:
- Wood Handling: In this section of the mill, teams cut, stack, load, debark, and chip logs before they are processed. Not only does their equipment have to handle the wood itself, but it also has to handle any dirt, rocks, and debris that enters the system during operation.
- Debarking Drums: To remove bark from logs, pulp and paper manufacturers use a cylindrical spinning machine known as a debarking drum, exposing its metal parts to high levels of abrasion and impact.
- Conveying Systems: Pneumatic conveyors, chutes, and other forms of transport equipment carry wood and wood chips throughout the production process, resulting in high levels of abrasion.
- Chipping & Processing: Not only is the chipping process itself very abrasive, but the hoppers and chutes that carry logs are subject to high levels of abrasion and impact.
Abrasion-resistant steel gives these pivotal pieces of equipment the durability they need to stay running longer. Without AR steel, repairs would occur more frequently, leading to increased downtime and higher unit costs.
The Role of Abrasion-Resistant Steel in Pulp & Paper Mills
We developed Tri-Braze® for pulp and paper mills that need the most reliable abrasion-resistant steel throughout their workflow. This specialized steel product offers superior hardness and toughness, making it highly resistant to impact and abrasion.
Today, our clients commonly use Tri-Braze® steel and Super-C® chromium carbide overlay plates in high-wear areas like log decks, debarking drums, and chipping systems.
Let’s take a deeper look at some of the most common use cases for AR steel products, including Tri-Braze® and Super-C®, within a pulp and paper mill.
- Wood Yard: Handling the Initial Load
Quite possibly the most demanding area in the mill is the wood yard; workers unload, sort, and prepare whole logs to be processed. In the wood yard, areas such as log decks, debarking drums, and conveyor systems experience some of the highest levels of wear and tear and are often good candidates for our proprietary Tri-Braze® steel. - Chipping & Processing: Durability Where It Counts
After removing bark from logs, they are cut into smaller pieces through processing and chipping. Chippers and chipper hoods are exposed to very high levels of abrasion. That’s why we have developed specialized chipper hoods made with Super-C® chromium carbide overlay plates. These specialized hoods offer incredible abrasion resistance, allowing them to last much longer than traditional options. - Bark & Waste Handling: Optimizing Efficiency
As you can imagine, bark and sawdust are two of the most common byproducts of processing wood into pulp and paper. Since mills produce such large quantities of these byproducts, they rely on specialized pieces of equipment to dispose of them. Tools like bark hogs, bark screws, and waste conveyors all move bark and sawdust throughout the mill, including into the plant’s power boilers. Operators use AR steel in key components of this equipment, such as bark hog hammers, which crush bark into smaller pieces. Pneumatic systems used to move bark chips and dust experience significant wear due to the speed and volume of conveyed materials. Ultra Tech 600 induction-hardened pipeline systems are an excellent choice to improve system longevity and reduce maintenance costs. - Caustic Plant & Lime Kiln: Facing Corrosion and Abrasion Head-On
The caustic plant and lime kiln are critical to the pulp-making process, allowing mill operators to produce chemicals necessary for production. Unfortunately, this equipment is exposed to high levels of both corrosive and abrasive materials. That’s why pulp and paper producers design key components for these machines, including grit screws and slaker rakes, out of specialized stainless steel that’s designed to resist both chemical corrosion and mechanical wear. - Caustic Plant & Lime Kiln: Facing Corrosion and Abrasion Head-On
The caustic plant and lime kiln are critical to the pulp-making process, allowing mill operators to produce chemicals necessary for production. Unfortunately, this equipment is exposed to high levels of both corrosive and abrasive materials. That’s why pulp and paper producers design key components for these machines, including grit screws and slaker rakes, out of specialized stainless steel that’s designed to resist both chemical corrosion and mechanical wear. - Power and Utilities: Extending Equipment Life
Many pulp and paper mills are at least partially powered by their own byproducts like bark, sawdust, and other organic waste. By transporting these byproducts to their boilers and burning them, mill operators can create their own source of power.
Because these byproducts can be so abrasive, equipment like ash hoppers, sand tanks, screw conveyors, and bucket elevators all require specialized parts made from steel that’s heat- and abrasion-resistant. Using the highest-quality steel from Tricon can help these pivotal parts of mill equipment last longer.
Custom Solutions from Tricon
In addition to our proprietary abrasion-resistant products, we also offer our customers a wide range of technical services, so they can be sure they’re getting the most out of AR steel.
If you don’t know where to start with AR steel, don’t worry. Our team can analyze the wear patterns and failure patterns of your current equipment, then suggest design modifications and materials to help you get the most out of your machinery.
Our expert technicians can help with a wide range of services: custom fabrication, ultrasonic testing, LiDAR scanning, and failure analysis.
Cost Savings Through Extended Equipment Life
Upgrading to Tricon’s AR steel can produce considerable cost savings over time. Although you’ll spend more upfront outfitting your equipment with Tricon’s premium abrasion resistant steels, the equipment will last much longer. This allows you to go longer between repairs, increasing efficiency and decreasing overall unit cost. Additionally, your employees will be working in a safer environment, as they will spend less time exposed to hazards while replacing broken or worn-out parts.
Case Study: Increasing Tonnage Without Increasing Costs
Are AR plates worth the investment? Here’s a customer success story of AR steel’s real-life impact.
Prior to working with Tricon, one of our customers in the pulp and paper industry was processing roughly 2,300 tons of wood per day in their mill. Prior to upgrading to abrasion-resistant steel in their equipment, their log decks would last roughly six years.
When they implemented a new wood yard, they also drove up their daily processing volume to roughly 8,000 tons of wood per day, putting increased strain on their equipment. They realized it was time to upgrade their log decks to Tri-Braze.
After they upgraded their equipment with Tricon steel, their log deck lasted roughly three years. With their volume more than tripled from previous operations, their log deck was able to operate 50% longer than their previous setup would have under this higher volume.
Tricon’s Impact on the Pulp & Paper Industry
The pulp and paper industry faces significant challenges thanks to the abrasive nature of the production process. Their equipment faces high levels of wear and tear throughout production, from wood handling and chipping to power generation, and they need the most reliable steel to withstand these forces.
Tricon Wear Solutions offers a wide variety of proprietary AR steel products that will help you get more out of your equipment by greatly extending usable life and allowing your mill to operate more efficiently. We’ve been helping pulp and paper mills achieve higher levels of reliability, sustainability, and cost savings for decades. Find out how we can help you gain a competitive advantage in this fast-paced industry.